Energy efficiency and reduction of climate change
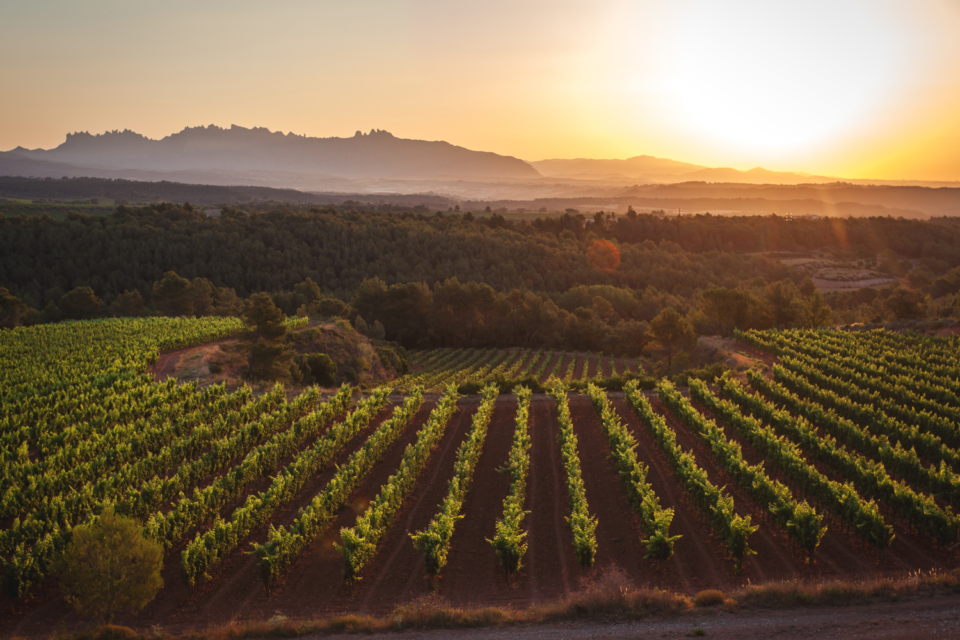
At the Freixenet Group we are currently focused on a double objective: to be more energy efficient and to contribute to counteracting the effects of climate change.
In order to reduce energy use, we have counters per section linked to control software. We are also carrying out energy audits that allow us to establish important reduction and improvement objectives.
In the same vein, in 2012 the Freixenet Group was one of the first companies in the cava sector to verify its Greenhouse Gas (GHG) emissions, in accordance with the ISO14064-1 standard.
With the integration of the calculation of the carbon footprint, within the ISO14001 Environmental Management System, at the Freixenet Group we measure our emissions and obtain new aspects of improvement that are integrated with the daily operations of our wineries. The objective of this integration process is to reduce CO2 emissions and contribute to the process of both mitigation and adaptation to climate change.
In this sense, it is important to highlight some of the actions carried out:
• In recent years we have opted for the purchase of energy of 100% renewable origin. This fact has allowed us to reduce our CO2 emissions from electricity consumption by about 2,000,000Kg CO2 eq.
• Efficiency in operations, specialization and centralization of production. Unique technological developments have enabled the automation of traditional operations at a very high level of efficiency. With this, it has achieved the centralization of product stocks in progress, the elimination of intermediate transport and artificial air conditioning and the reduction of emissions. Results: the capacity of the cellars has increased by 32.2%, the dispersion of product stocks in progress has been reduced by 64% and 10,45th freight truck trips per year are avoided, equivalent to 188,140 KM fewer trips. per year or 545 T CO² less emitted per year.
• In 2012, the use of diesel for combustion and generation of hot water was eliminated and replaced by natural gas, in addition to replacing automotive diesel forklifts with LPG forklifts. Result: 96% reduction in NOx emissions, 99% reduction in particle emissions, 50% reduction in noise levels, 10% reduction in CO2 emissions.
• Investment in new, more efficient and sustainable equipment, especially cold equipment.
• Install heat exchangers to take advantage of the smoke heat from the boiler and the cold from the cellar processes.
• Savings of 40% of electrical energy consumed in the process office air conditioning by replacing electric air conditioning.
• Replacement of conventional luminaires with state-of-the-art fluorescent LEDs. They consume 51% less.
• Awareness and sensitization of the staff to promote energy saving and efficiency.